When it comes to materials that can endure the unforgiving conditions of marine environments, copper stands out for its exceptional durability and natural corrosion resistance. Saltwater, moisture, and biofouling are constant threats to most metals, but copper has unique properties that allow it to perform remarkably well in these settings.
This article explores the science behind Copper and Marine Corrosion Resistance, highlighting why it’s a top choice for marine applications. Whether you’re a marine engineer or a copper supplier seeking to understand its technical edge, you’ll gain valuable insight into why copper continues to be a trusted material across coastal industries.
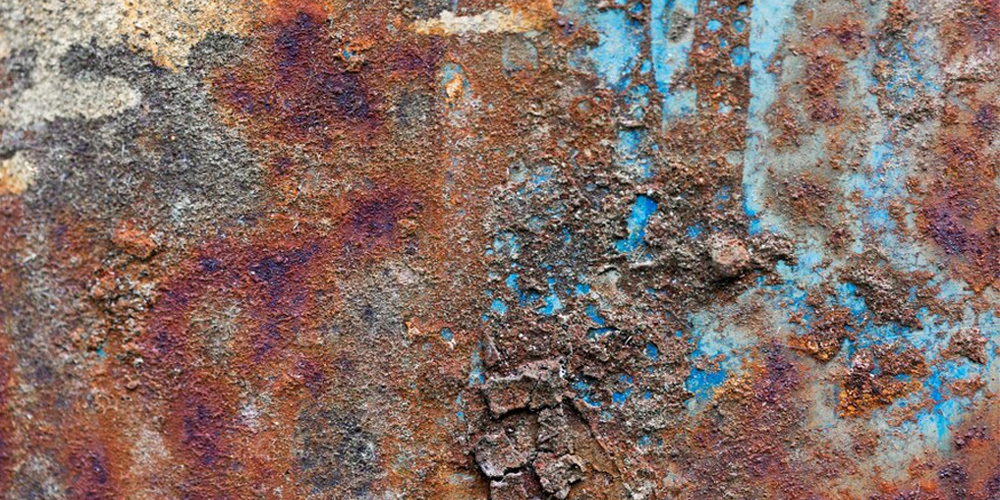
Understanding Marine Corrosion: A Harsh Test for Metals
Marine environments are among the most challenging for metal durability due to their complex and aggressive nature. Saltwater is highly conductive and contains chlorides that actively attack the surface of metals, disrupting their structural integrity over time. Oxygen in the water supports electrochemical reactions that drive the corrosion process, particularly in areas where water movement enhances oxygen exposure like tidal and splash zones.
Humidity in the marine atmosphere increases the risk of atmospheric corrosion even in coastal areas far from direct contact with seawater. Moreover, biological factors such as algae, barnacles, and bacteria can accelerate corrosion by creating localized areas of chemical concentration or by physically damaging protective coatings. These combined effects can quickly degrade metals like steel and aluminum unless they are specifically designed or treated for marine use. Protective coatings, sacrificial anodes, and corrosion resistant alloys are often required to prolong the lifespan of traditional metals in these conditions.
Copper’s Natural Resistance to Marine Corrosion
Copper forms a stable, adherent oxide layer primarily cuprous oxide (Cu2O) on its surface when exposed to air, moisture, and seawater. This layer, known as a patina, acts as a protective shield by significantly slowing the penetration of corrosive agents such as chloride ions present in saltwater. Over time, this patina thickens and becomes more effective, making copper even more resistant the longer it is in use.
What sets copper apart is the uniform and self-healing nature of this protective layer. Unlike many metals that suffer from localized attacks such as pitting or crevice corrosion, copper tends to corrode evenly. If the oxide layer is scratched or damaged, it can regenerate under normal atmospheric or marine exposure, continuing to provide defense against corrosion. Additionally, copper’s corrosion resistance is enhanced by its low reactivity with seawater’s dissolved oxygen and the natural antimicrobial properties that reduce biofouling. This resistance not only extends the service life of copper-based components but also reduces maintenance needs and operational downtime key advantages in marine operations.
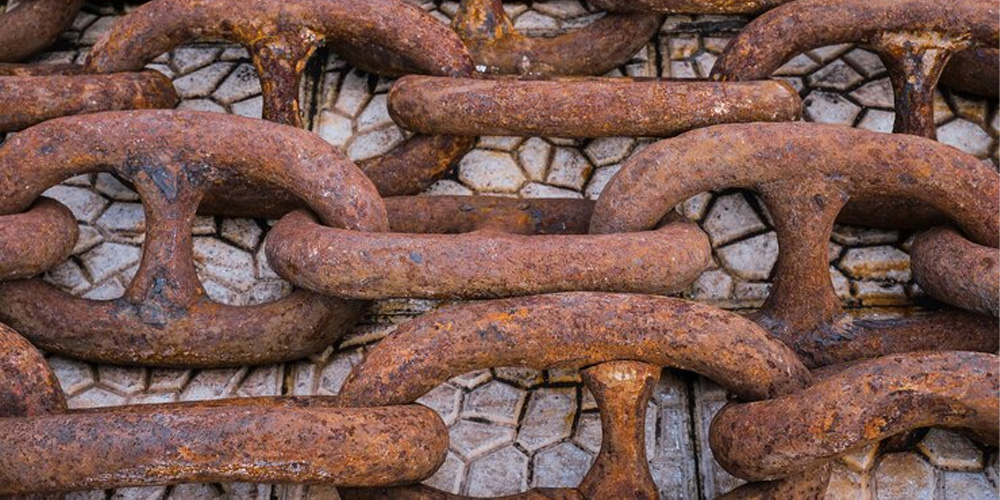
Scientific Reasons Behind Copper’s Durability
Copper’s impressive durability in marine environments stems from its atomic structure and inherent chemical properties. Its relatively low standard electrode potential means it is less likely to participate in electrochemical reactions with chloride ions, a primary cause of corrosion in saltwater environments. Unlike metals such as iron or zinc, copper maintains its integrity even when exposed to aggressive agents in seawater.
Furthermore, copper’s antimicrobial nature prevents the buildup of biofilms, barnacles, and other marine organisms that can contribute to localized corrosion. This makes copper and its alloys particularly useful for underwater surfaces or components exposed to marine life. In addition to its corrosion resistance, copper’s high thermal and electrical conductivity ensures efficient heat dissipation and reliable electrical performance. This makes it an optimal material not just for structural parts but also for wiring and electronic components in marine systems, where consistent performance is essential.
Applications of Copper in Marine Environments
Copper is widely used in the maritime sector for components such as pipes, heat exchangers, hulls, and propellers. These applications benefit from copper’s ability to resist corrosion and biofouling over long periods, even under continuous saltwater exposure. In particular, copper rod is utilized in the manufacturing of marine-grade connectors, grounding systems, and structural reinforcements in electrical equipment, owing to its mechanical strength and resistance to both electrical degradation and corrosion. Copper is also commonly found in plumbing systems aboard ships and offshore platforms due to its resistance to microbial influenced corrosion (MIC). Moreover, in the form of sheathing and hull cladding, copper plays a vital role in protecting submerged surfaces from fouling organisms and chemical deterioration.
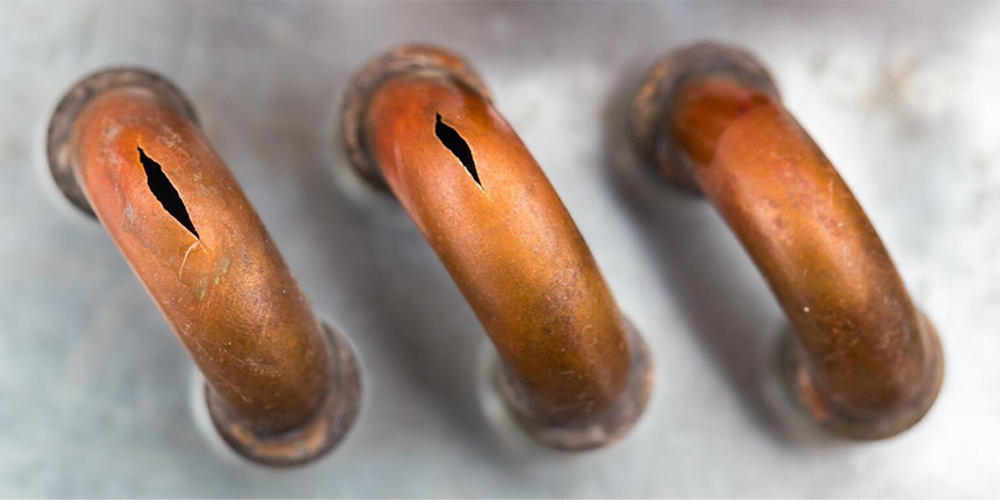
Comparing Copper to Other Metals in Saltwater Environments
When compared to materials like stainless steel or aluminum, copper consistently performs better in terms of corrosion resistance. For example, copper wire used in shipboard electrical systems tends to outlast similar-sized aluminum wires in salt-laden atmospheres.
Challenges and Considerations When Using Copper at Sea
Despite its many benefits, using copper in marine environments comes with a few important considerations that directly relate to Copper and Marine Corrosion Resistance:
Higher Cost: Copper is generally more expensive than alternatives such as aluminum or some coated steels. This can impact budget-sensitive projects or large scale applications.
Increased Weight: Copper is denser than many other commonly used materials, which may not be ideal for vessels or systems where weight reduction is a priority.
Galvanic Corrosion Risk: When copper is in contact with less noble metals (like zinc, aluminum, or steel) in a conductive and wet environment, galvanic corrosion can occur. This type of corrosion may lead to premature failure of the less noble metal unless proper electrical isolation or protective coatings are applied.
Design Complexity: Integrating copper with other materials in marine systems often requires careful planning. Special attention must be given to the choice of connectors, fasteners, and joint materials to prevent corrosion-related compatibility issues.
Environmental Considerations: In some coastal areas, regulations may limit the use of copper due to concerns about metal runoff and its potential impact on aquatic ecosystems. Compliance with local environmental guidelines is essential.
Understanding and mitigating these challenges can help marine engineers and designers make the most of copper’s advantages while ensuring long-term system reliability.
Future Innovations: Copper Alloys and Marine Tech
The development of advanced copper alloys like cupronickel has further expanded copper’s role in the marine industry. These alloys provide enhanced strength, antimicrobial resistance, and corrosion protection making them ideal for next generation maritime applications.
Conclusion: Why Copper Remains a Trusted Choice in Marine Engineering
The exceptional properties of copper make it a material of choice in harsh marine environments. Its ability to resist corrosion, combined with its versatility and longevity, ensures its continued relevance in modern marine engineering. From basic infrastructure to high-tech systems, Copper and Marine Corrosion Resistance remains a cornerstone of maritime innovation.
If you’re looking to source high quality copper products for your marine or industrial needs such as 1.8 mm copper rod, 2.6 mm copper rod, or 8 mm copper rod you can rely on Kayhanmetal. As a trusted supplier in the copper industry, Kayhan Metal provides top-grade materials with fast international shipping and competitive pricing.
FAQ
What happens during the copper and salt water reaction?
When copper is exposed to saltwater, it undergoes a mild oxidation process that forms a protective oxide layer on its surface. This layer, typically composed of cuprous oxide (Cu₂O), acts as a natural barrier against further corrosion, making copper highly resistant to the aggressive effects of saltwater environments.
Why are copper alloys in seawater effective in avoiding corrosion?
Copper alloys, such as cupronickel and bronze, are engineered for enhanced durability in marine environments. These alloys combine copper’s corrosion resistance with additional mechanical strength and resistance to biofouling, making them ideal for use in seawater applications where long-term performance is critical.
Does copper corrode in saltwater?
Copper does not corrode in saltwater the same way many other metals do. Instead of rapid degradation, it develops a stable and uniform protective layer that significantly slows corrosion. This is one of the key reasons for the popularity of Copper and Marine Corrosion Resistance in maritime industries.
Does copper dissolve in water?
Pure copper does not dissolve in water under normal conditions. It is highly stable in both freshwater and saltwater due to its low solubility and strong resistance to chemical breakdown. This property contributes to its longevity and reliability in marine applications.
What is the best metal for saltwater environments?
While several metals are used in marine settings, copper and its alloys are among the best for resisting corrosion in saltwater. Other good choices include stainless steel and titanium. However, copper stands out for its natural antimicrobial properties and self-healing oxide layer.
No comment