In the world of engineering and advanced industries, selecting durable and reliable raw materials plays a crucial role in the longevity and quality of products. Among the metals that have always stood out due to their mechanical and physical properties is copper. In this article, we explore the concept of Copper and Pressure Resistance and analyze its importance across various industrial applications.
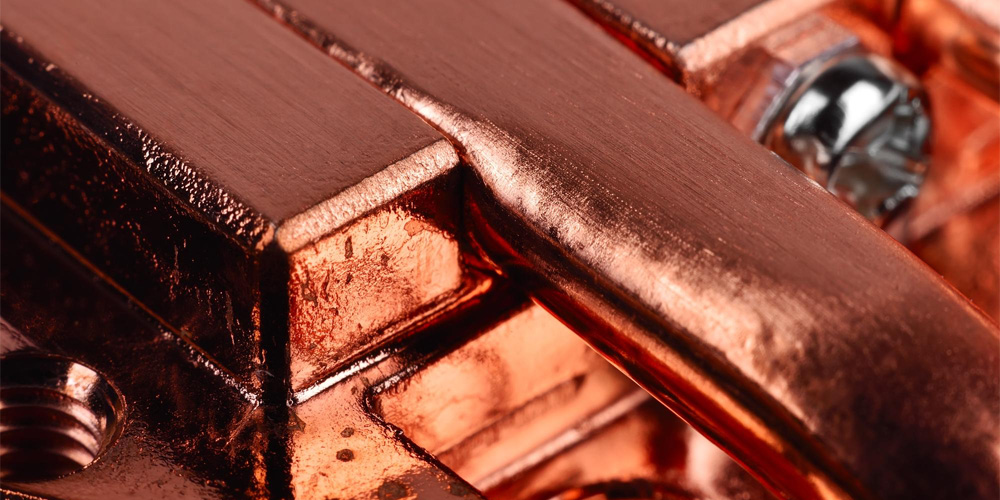
What Is Copper and Pressure Resistance and How Is It Measured?
Copper’s pressure resistance refers to its ability to withstand external forces without undergoing permanent deformation or structural failure. This property is measured using standard pressure tests such as those outlined by ASTM or ISO. During these tests, a sample of copper is subjected to either constant or variable compressive forces until deformation or fracture occurs.
Scientifically, copper’s compressive strength typically falls between 210 and 250 MPa, though this range can vary depending on purity, heat treatment, and the original forming method. Copper alloys such as brass and bronze show different pressure resistance levels, making them suitable for specific applications. One common question is: “Does copper have high resistance?” The short answer is: copper exhibits moderate to high pressure resistance, especially when alloyed or used in engineered structures. As such, in applications requiring both mechanical strength and excellent conductivity, copper is a premium choice.
The Atomic Structure of Copper and Its Effect on Pressure Resistance
Copper has a face-centered cubic (FCC) crystal structure one of the most stable configurations among metals. This structure enables copper to endure significant pressure without fracturing. The atomic arrangement in FCC allows stress to distribute evenly across the lattice, reducing stress concentration points and enhancing the metal’s resilience under load.
Moreover, the ease of dislocation movement in copper’s FCC structure allows it to absorb compressive energy through temporary deformation, rather than fracturing. This behavior is key to copper’s performance under high-pressure environments and highlights why it is often selected for components that must maintain mechanical integrity under stress.
Comparing Copper’s Pressure Resistance with Aluminum and Steel
While steel offers significantly higher compressive strength and is used in heavy-duty structures, it comes with drawbacks such as higher weight and lower corrosion resistance. On the other hand, copper, despite having a lower pressure resistance than steel, provides better corrosion resistance, thermal conductivity, and is easier to machine and solder.
Compared to aluminum, copper is much heavier but stronger. Aluminum’s low density makes it ideal for aerospace and transport applications, yet when high-pressure resistance is needed, copper performs better. It also remains more thermally stable than aluminum at elevated temperatures an advantage in systems like industrial heat exchangers. When analyzing technical parameters such as copper units of pressure, it’s clear that copper combines moderate to high pressure tolerance with electrical conductivity and corrosion resistance, making it a versatile choice across engineering applications.
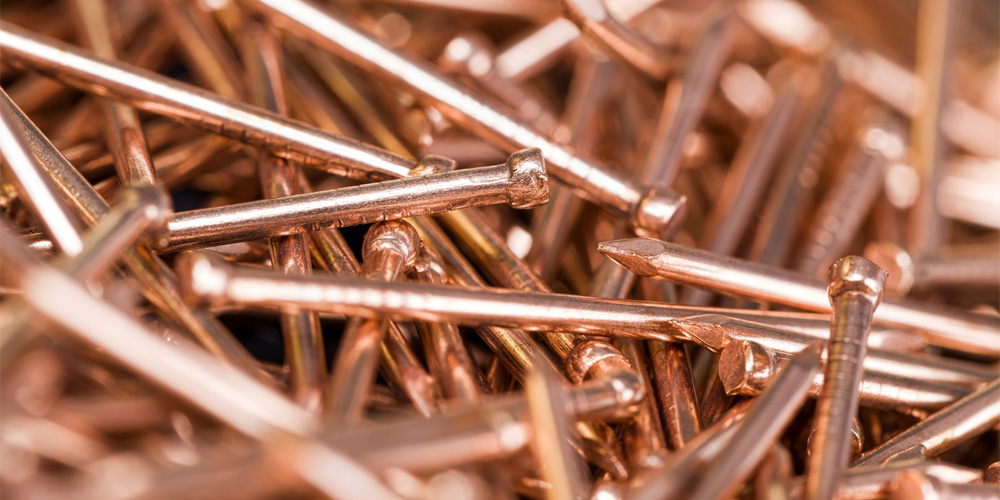
Industrial Applications of Copper and Pressure Resistance
Due to its strong resistance to compression, copper is widely used in the manufacturing of pipes, connectors, and high pressure fittings. Industries such as HVAC systems, hydraulic equipment, and high pressure pipelines rely on copper’s durability. Components like pumps, valves, industrial cylinders, and heat exchangers benefit from copper’s ability to withstand both pressure and corrosion.
In the construction industry, copper pipes are preferred for transporting hot and cold water, offering both sanitary and mechanical advantages. In oil and gas, copper is used in components that require both high-pressure tolerance and thermal conductivity. A leading copper rod supplier often emphasizes this pressure resistant characteristic as a key competitive advantage over alternative metals.
Role of Copper and Pressure Resistance in Industrial Cables and High Pressure Equipment
In heavy industries and advanced engineering projects, electrical cables and components are often subjected to intense mechanical and thermal stress. In these settings, selecting the right material is crucial for operational reliability. Copper is considered one of the best options for high-pressure cable production due to its pressure resistance, excellent conductivity, and structural flexibility.
In industrial copper wire production, this pressure resistance ensures the cable can endure compressive, tensile, and impact forces. These wires are widely used in tunnels, power plants, steel mills, and offshore platforms. Likewise, copper rod is used in the manufacturing of mechanical and electrical components exposed to high pressure conditions such as connectors, terminals, bushings, and power rails ensuring both safety and extended product lifespan.
Copper and Pressure Resistance in Automotive and Aerospace Industries
In high-tech industries like automotive and aerospace, components must withstand not only extreme pressures but also vibrations, temperature fluctuations, and harsh environments. Copper stands out due to its combination of mechanical strength, high thermal conductivity, and precision machinability.
In vehicles, copper is used in radiators, cooling systems, pressure resistant sensors, and wiring harnesses. In aerospace where weight, safety, and durability are critical copper’s pressure resistance enhances the longevity and stability of key electronic components in aircraft and satellites. An added benefit is the reduction in maintenance costs and higher system efficiency.
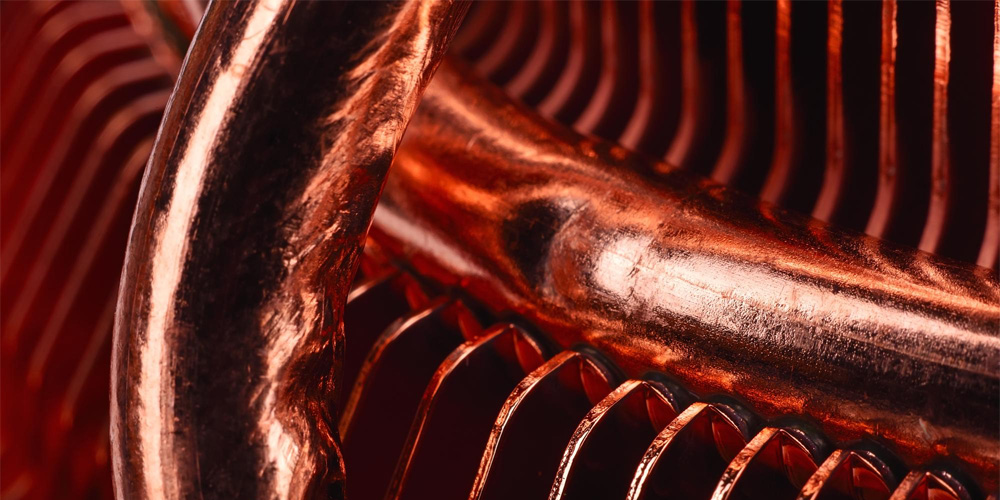
Challenges and Limitations of Copper and Pressure Resistance
Despite its many benefits, copper presents a few limitations in specific applications. Its higher weight compared to advanced materials like aluminum or titanium can be a drawback where weight reduction is a priority. Also, in situations demanding extremely high compressive strength, certain superalloys may outperform copper.
Another consideration is copper’s relatively high cost, which may limit its use in budget-sensitive projects especially those requiring large volumes of material. Nevertheless, copper’s exceptional durability and 100% recyclability often offset the initial investment over the product’s life cycle.
Conclusion: Why Copper and Pressure Resistance Is a Key Material Selection Factor
Based on extensive analysis, Copper and Pressure Resistance plays a vital role in industrial, electrical, and mechanical design. Combined with other advantages such as high conductivity and corrosion resistance copper becomes a smart and strategic material choice across various industries.
In today’s world, where sustainability, efficiency, and cost optimization matter more than ever, selecting materials with pressure resistance can significantly improve the lifespan and performance of end products. If you’re looking for premium copper products with global standards, Kayhanmetal is one of the most trusted suppliers in the field. We proudly offer various sizes of copper rods, including Copper rod 8 mm, Copper rod 2.6 mm, Copper rod 1.8 mm. Whether you’re in industrial manufacturing, cable production, automotive engineering, or construction, we’re ready to meet your needs with guaranteed quality, competitive pricing, and fast delivery. With technical expertise, a robust international supply network, and a deep commitment to excellence, Kayhanmetal has become a reliable name in the global copper market. For expert consultation or to place an order, feel free to contact our team today.
No comment