In today’s rapidly advancing world of industry and technology, the methods of producing raw materials have also been significantly optimized. One of the most efficient and modern techniques is the Continuous Casting of Copper Rod. This process has enabled manufacturers to reduce waste, improve quality, and increase production speed, playing a vital role in the global market.
If you are a buyer or manufacturer looking to familiarize yourself with the latest copper production processes or seeking a reliable copper supplier, this article is for you.
In the following sections, we will dive deep into the continuous cast copper rod manufacturing process, compare it with traditional methods, and explore the advantages, challenges, and applications of copper rods produced with this technology. Stay with us to learn everything you need to know about continuous casting of copper rod.
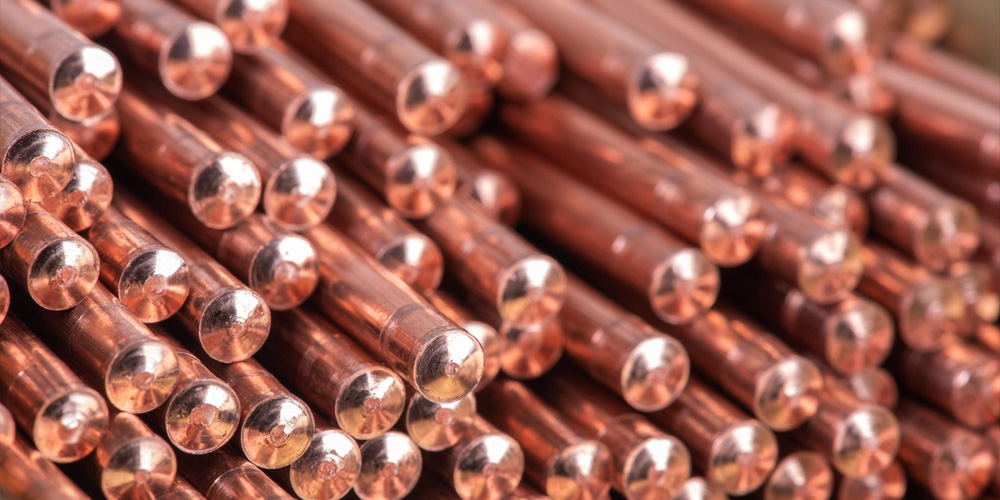
What Is Continuous Casting of Copper Rod?
Continuous Casting of Copper Rod is an industrial process where molten copper is continuously cast into rods of specific dimensions. Unlike traditional batch casting methods, in this technique, the copper flows without interruption into special molds, rapidly cools down, and solidifies into rod form.
In fact, continuous casting of copper rods has revolutionized the wire and cable manufacturing industry by enhancing productivity and improving the quality of final products.
How Does the Continuous Casting Process Work?
The Continuous Casting of Copper Rod involves several key stages. First, pure copper is heated above its melting point. The molten copper is then poured into specialized molds. During this stage, the temperature and flow rate are precisely controlled to form the copper rod.
After exiting the mold, the rod is gradually cooled and then passes through rolling mills to achieve standard diameters and properties. This method, known as the continuous cast copper rod manufacturing process, significantly saves time, energy, and production costs.
Manufacturers typically use the latest casting equipment to ensure final product quality. If you want to know more about the specifications of different copper rods, you can refer to the product sections of reputable copper rod suppliers’ websites.
Continuous Casting vs Traditional Methods
One of the most notable advantages of continuous casting over traditional methods is the superior consistency and structural integrity of the products. In conventional techniques, issues like air pockets, surface cracks, and impurities were more common. However, in the Continuous Casting of Copper Rod, better control over cooling and solidification results in higher quality outputs.
Moreover, by eliminating extra steps such as initial casting and repeated rolling, this method dramatically reduces both production costs and lead time.
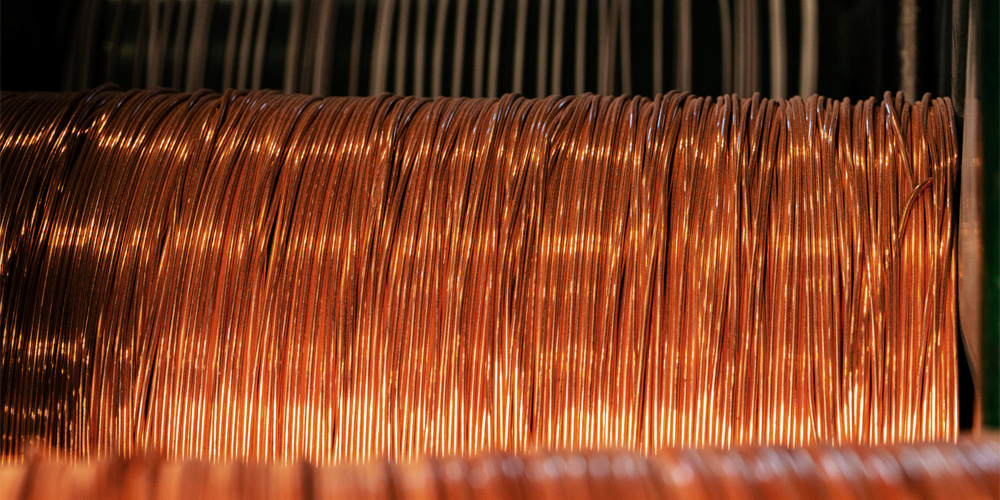
Advantages of Continuous Casting in Copper Rod Production
The Continuous Casting of Copper Rod process offers numerous advantages, making it the first choice for many leading manufacturers worldwide. Here are the key benefits:
Consistent Product Quality
Due to precise control of temperature and cooling speed, rods produced through continuous casting feature uniform structures, free from cracks, voids, or impurities. This ensures superior electrical and mechanical performance, making them ideal for critical industrial applications.
Reduced Energy Consumption and Production Costs
One major advantage is the significant energy savings. By eliminating unnecessary steps like initial casting, repeated rolling, and recycling defective materials, operating costs are substantially reduced particularly in large-scale production.
High-Speed Production
Continuous casting allows uninterrupted production, enabling the manufacturing of long copper rods quickly. This high speed facilitates meeting the demands of high consumption markets and shortens delivery times.
Minimized Waste and Scrap
The strict process control minimizes production waste, resulting in higher material efficiency. This not only boosts profitability but also brings environmental benefits.
Industrial Scale and Export Capability
Continuous casting supports mass production without compromising quality. This enables companies to supply domestic markets and expand into international exports. High and consistent product quality has made continuously cast copper rods highly popular among foreign clients.
Additionally, copper rods produced by this method are ideal for manufacturing premium copper wire used extensively in the power, electronics, automotive, and telecommunications industries.
Machinery and Equipment Used in Continuous Casting
The main equipment involved in the Continuous Casting of Copper Rod process includes induction melting furnaces, water-cooled copper molds, rapid cooling systems, initial rolling mills, and product collection systems.
These machines must ensure high precision and durability to maintain uninterrupted and consistent quality production.
In many modern production lines, digital monitoring systems are employed for precise temperature and flow control. One of the critical components of these lines is the continuous casting rod machine, which ensures defect free copper rod production.
Final Quality of Continuously Cast Copper Rods
Copper rods produced by continuous casting exhibit a smooth surface, high density, and low electrical resistance. These properties make them ideal for manufacturing electrical wires, industrial cables, and telecommunications equipment.
The outstanding quality of these rods has earned them a special place in global markets, with growing demand from diverse industries.
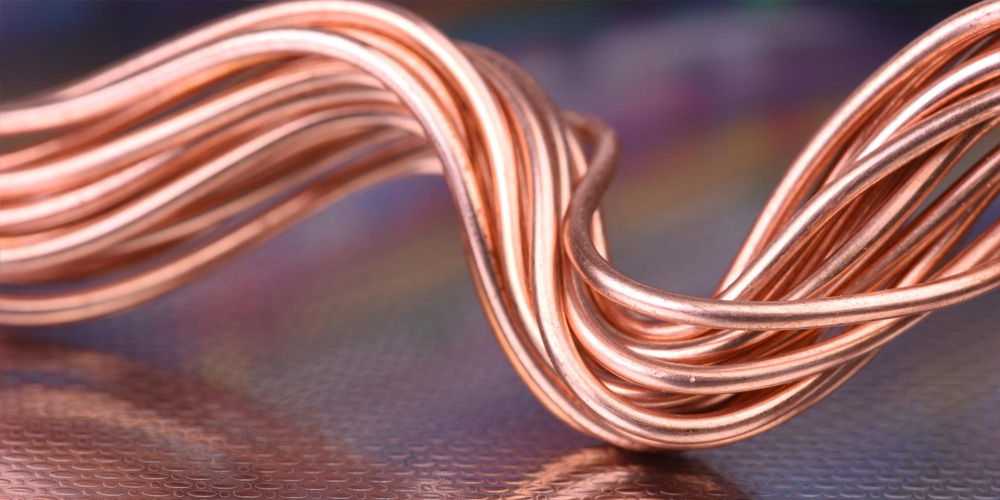
Applications of Continuously Cast Copper Rods
Copper rods manufactured through the Continuous Casting of Copper Rod process are widely used across various key industries due to their consistent quality, excellent conductivity, and high durability. Here are some major applications:
Electrical and Electronics Industry
The largest share of copper rod consumption lies in the power sector. They are used to produce electric wires, power transmission cables, low-voltage distribution cables, and electrical components. High conductivity ensures minimal energy loss and extended service life.
Automotive Industry
With the rise of electric and hybrid vehicles, the demand for high-quality wiring has soared. Continuously cast copper rods, thanks to their flexibility and corrosion resistance, are ideal for producing automotive wiring systems, control units, and batteries.
Construction Industry
In construction projects, ensuring reliable energy supply and safety is crucial. Copper rods are used in building electrical systems, HVAC (Heating, Ventilation, and Air Conditioning) installations, grounding systems, and fire alarm cables. High-quality copper enhances building safety and reliability.
Telecommunications Industry
In today’s connected world, communication cables require high transmission speeds and stability. Continuously cast copper rods serve as the core of data cables, internet cables, telephone wires, and network cables, improving the performance of telecommunication systems.
Challenges and Limitations of Continuous Casting
Despite its many advantages, continuous casting faces some challenges. Precise control of mold temperature and casting speed demands advanced equipment and skilled personnel. Any errors in the process can result in defective or unstable rods.
Additionally, the initial investment required to establish continuous casting lines is higher compared to traditional methods.
Conclusion: Why Continuous Casting Is the Future of Copper Rod Production
Ultimately, Continuous Casting of Copper Rod stands out as the future of copper rod production due to its efficiency, superior product quality, and resource optimization.
As the electrical, automotive, and telecommunications industries continue to grow, the demand for high-quality copper rods is rapidly increasing, rendering traditional production methods inadequate.
Adopting continuous casting technology offers an exceptional opportunity for manufacturers to strengthen their competitiveness in global markets.
If you are looking to source premium copper products such as copper rod 1.8 mm, copper rod 2.6 mm, and copper rod 8 mm, get in touch with the trusted team at Kayhanmetal today. Our sales team is ready to provide you with the finest products backed by quality assurance, competitive pricing, and fast delivery.
No comment