In the modern world, copper wires are a fundamental component in industrial, construction, and electronic infrastructures. These wires must endure harsh environmental conditions, mechanical stress, and continuous vibrations. One of the most influential factors in the longevity and performance of wires is metal fatigue resistance a property in which copper excels. In this article, we take a closer look at Copper and Fatigue Resistance to understand why this feature is the key to the exceptional durability of copper wires. This topic is particularly crucial for manufacturers and copper wholesalers aiming to deliver high quality, long lasting products.
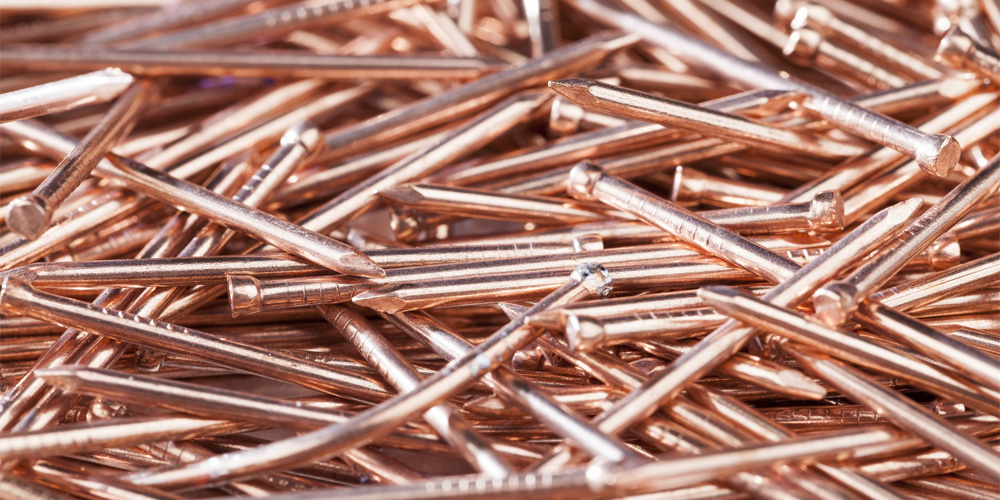
What Is Copper and Fatigue Resistance and Why Is It Important?
Fatigue resistance refers to a metal’s ability to withstand repeated, cyclic, and vibrational loads without developing early cracks or failing. This kind of stress occurs when a material is exposed to fluctuating or repetitive forces over time, leading to internal structural weakening.
In many industrial applications such as electrical cables, automotive wiring, or electronic equipment fatigue can result in malfunction, safety hazards, and complete system failure. That’s why selecting materials with high fatigue resistance is essential.
When we talk about Copper and Fatigue Resistance, we refer to copper’s ability to resist these mechanical stresses. Due to its stable crystal structure, excellent ductility, and ability to endure repeated strain without losing mechanical properties, copper performs remarkably well. These characteristics allow copper wires to remain crack free and structurally sound, even under demanding working conditions. As a result, fatigue resistance is one of the main reasons copper is the preferred choice in critical and long term industrial applications.
The Impact of Metal Fatigue on the Performance and Safety of Conductive Wires
Metal fatigue gradually causes microcracks within a material due to recurring mechanical stress. Initially invisible, these cracks grow over time and can lead to sudden failure. In conductive wires, fatigue directly affects electrical performance and system safety. Cracks can increase resistance, cause voltage drops, interrupt current flow, create sparks, or even lead to fires. In environments like industrial power panels, vehicles, airplanes, or power plants, such risks can have severe consequences.
That’s why using metals with high fatigue resistance, like copper, is vital in designing safe and reliable energy transmission systems. Copper and Fatigue Resistance not only extends the service life of wires but also ensures stable performance and safety in electrical equipment.
Advantages of Copper Over Other Metals in Fatigue Resistance
Copper has long been recognized as one of the best conductive materials, but its benefits go beyond electrical conductivity. One of its key mechanical features is high fatigue resistance, which distinguishes it from other metals like aluminum, steel, and nickel.
Copper combines softness, mechanical flexibility, high conductivity, and sufficient structural strength. This unique mix allows it to absorb and distribute cyclic stress effectively without cracking or failing prematurely.
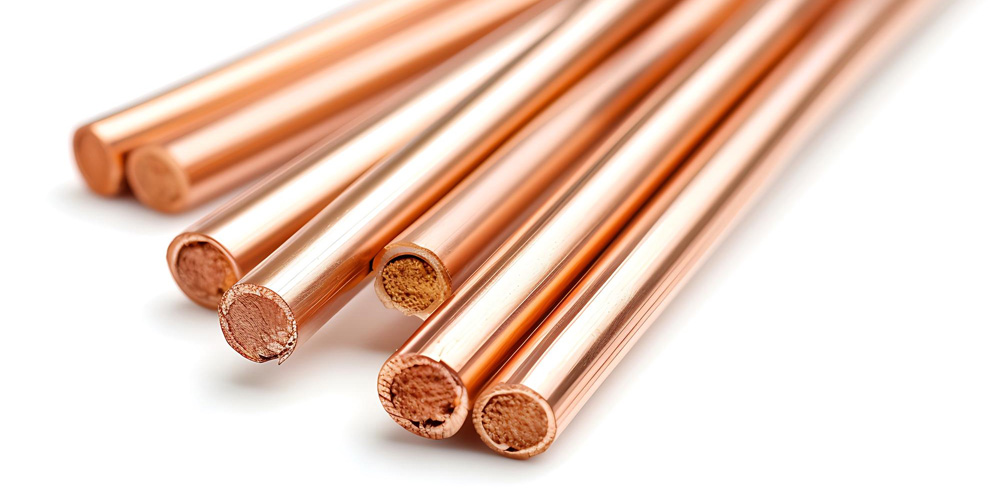
Comparison with Other Metals:
- Aluminum: Lighter but has a shorter fatigue life.
- Steel: Strong but harder and with lower conductivity.
- Nickel: Heat resistant but less cost effective and conductive compared to copper.
As a result, copper wires are a reliable and economical choice for industrial cables, electronic systems, automotive wiring, and power transmission lines.
The Role of Copper and Fatigue Resistance Across Industries
Copper and Fatigue Resistance is a major advantage in various high tech and mission critical industries. This property allows copper to withstand cyclic and vibrational stress, which is essential for durability and safety in industrial applications.
- Aerospace: Cables and electrical connectors are exposed to constant vibrations, extreme temperatures, and variable pressure. High fatigue resistant copper wire ensures stable power and signal transmission in critical systems such as navigation and communications.
- Automotive: Vehicle wiring must withstand mechanical shocks, temperature fluctuations, and repeated bending. Copper’s mechanical stability and flexibility make it ideal for safety and control systems.
- Rail Transport: Energy cables and control systems must operate reliably under intense vibration, constant stress, and over long distances. Copper’s fatigue resistance ensures long-term performance.
- Construction and Urban Infrastructure: Copper wires are widely used in urban projects, high rise buildings, and power distribution networks where reliability, safety, and longevity are vital.
- Renewable Energy: In wind turbines and solar panels, cables experience continuous mechanical and thermal stress. Products like copper rod and specialized fatigue resistant wires ensure consistent performance and minimal maintenance.
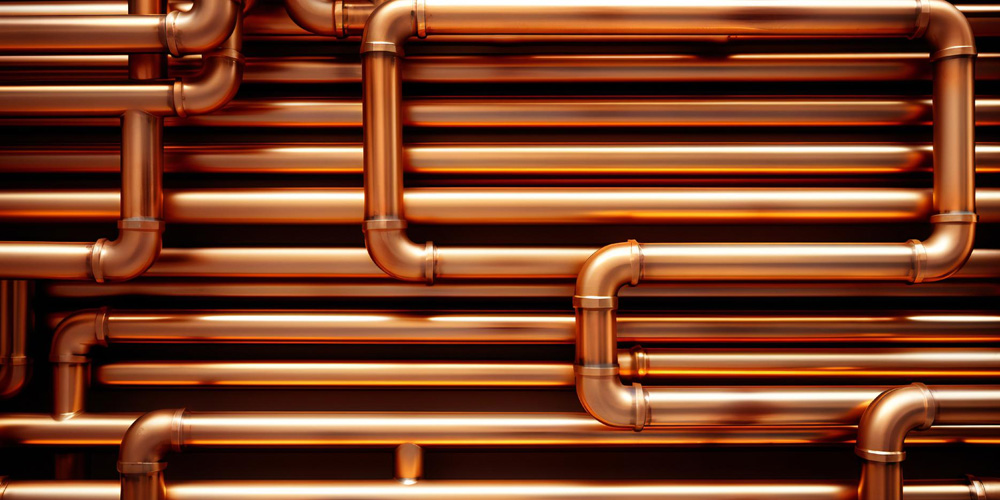
How Copper and Fatigue Resistance Reduces Maintenance and Extends Lifespan
When a wire can operate under high stress environments without frequent replacements, operational costs decrease. Copper provides exactly this benefit. With fewer failures, less emergency repair, and higher system efficiency, it becomes the smart choice for long term projects.
Production Methods of Fatigue Resistant Copper Rods
To achieve maximum Fatigue Resistance in copper wires and rods, production processes and material treatment play a crucial role. Several types of copper products are manufactured based on usage requirements:
- ETP Copper Rod (Electrolytic Tough Pitch): Produced via electrolysis, offering high conductivity and 99.9% purity. Suitable for general electrical and cabling applications, though its fatigue performance is moderate.
- Annealed Copper Rod: These rods are heat treated and softened after rolling to improve flexibility and formability, enhancing their resistance to cyclic mechanical stress.
- Oxygen Free Copper: Manufactured with extremely low oxygen content, it offers superior electrical and thermal conductivity along with excellent resistance to fatigue and corrosion. Ideal for precision electronics, aerospace, and medical applications.
Conclusion: Why Copper’s Fatigue Resistance Makes It a Smart Choice for Wires
As we’ve seen, Copper and Fatigue Resistance is not just a mechanical feature it’s a determining factor in the performance and safety of wires. Copper’s ability to withstand repeated mechanical stress makes it the ideal material for demanding environments and long lasting applications.
For high quality copper products such as 1.8 mm copper rod, 2.6 mm copper rod, and 8 mm copper rod, you can contact Kayhanmetal, a trusted industry supplier.
No comment